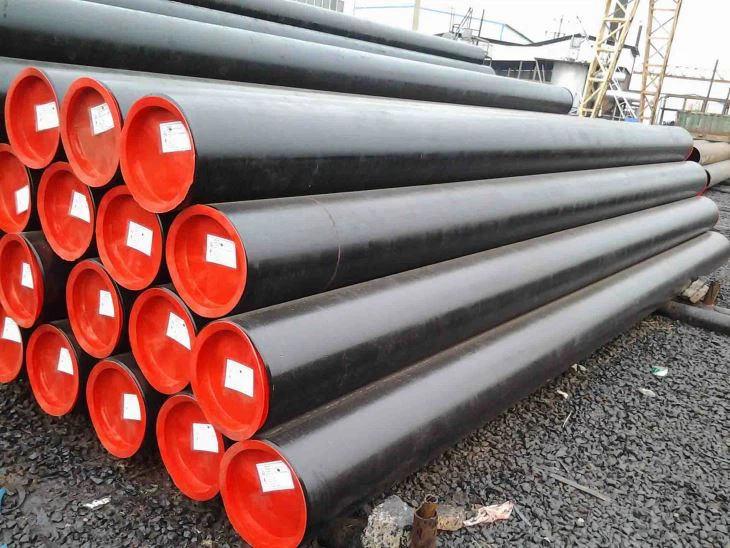
Seamless Tube Sour Service NACE MR 0175 12" SCH40 12M length
NACE MR 0175 ISO15156is a Materials Standard issued by the National Association ofCorrosionEngineers It is originally
Product Introduction
NACE MR 0175/ISO 15156 is a Materials Standard issued by the National Association of Corrosion Engineers.
It is originally a US standard intended to assess the suitability of materials for oilfield equipment where sulphide (sulfide) stress corrosion cracking may be a risk in hydrogen sulphide (sour) environments. However, the world standards body ISO has issued it under its own "brand". The latest edition includes technical corrigenda from 2005.
The standard specifies the types of corrosion resistant materials including stainless steel that can be used in specific oilfield environments and places limits on the hardness of the material. This applies both to parent and weld material. The maximum hardness is usually defined in terms of the Rockwell 'C' scale.
No conversion to other hardness scale is given in MR 0175 which presents one problem as softened stainless steel hardness are measured using either the Rockwell 'B', Vickers or Brinell scales. Approximate conversions are available.
Summary of MR 0175 Requirements
A wide range of materials is covered by the standard including most types (families) of stainless steel. The table below shows some of these grades. However, this summary is intended to only give a general idea of this complex standard and is not a substitute for the original document.
NACE MR0175 and MR0103 Standard
The NACE MR0175 Standards Metals for Sulfide Stress Cracking and Stress Corrosion Cracking Resistance in Sour Oilfield Environments. also known as ISO15156 (International Standard), was developed for the prevention of sulfide stress cracking due to H2S in oil and gas production systems. Historically, for the refining process, the MR0175 standard was used as a guideline for choosing suitable materials. However, the refining process environment is outside of the scope of the MR0175 standard. The NACE MR0103 standard was developed to be a refinery-specific sour service materials standard. Like the MR0175 standard, the MR0103 standard provides recommendations on which alloys and materials to use to prevent sulfide stress cracking in an H2 S containing environment
Steel Type | Grades Included | Comment |
Ferritic | 405,430, 409, 434, 436, 442, 444, 445, 446, 447, 448 | Hardness up to 22 HRC |
Martensitic | 410, 420 | Hardness up to 22 HRC |
Martensitic | F6NM | Hardness up to 23 HRC |
Martensitic | S41425 | Hardness up to 28 HRC |
Austenitic | 201, 202, 302, 304, 304L, 305, 309, 310, 316, 316L, 317, 321, 347, S31254(254SMO), N08904(904L), N08926(1925hMo) | Solution annealed, no cold work to enhance properties, hardness up to 22 HRC |
Austenitic | S20910 | Hardness up to 35 HRC |
Duplex | S31803 (1.4462), S32520 (UR 52N+),S32750 (2507), S32760 (Zeron 100), S32550(Ferralium 255) | PREN >30 solution annealed condition, ferrite content 35% to 65%, or 30 to 70% in welds. Note that the general restriction of 28 HRC in previous editions is not found in this latest edition of the standard. There is a specific restriction on HIP'd S31803 to 25HRC. For some applications cold worked material is allowed up to 36HRC |
Precipitation Hardening |
17-4 PH | 33 HRC Age hardening at 620 deg C |
Precipitation Hardening | S45000 | 31 HRC Age hardening at 620 deg C |
Precipitation Hardening | S66286 | 35 HRC |
Free machining grades such as the 303 and 416 types are excluded from of NACE MR 0175/ISO 15156
ASTM SCOPE:
Product Knowledge: There is a clear boundary between the application of these two Material Requirement (MR) specifications: the fence of the refinery. Both of these MR specs have the same end goal: to reduce the occurrence of cracking from sulphide stress corrosion cracking. This is generally done by reducing the amount of stress applied to the material (including residual stresses) or by only using alloys that are inherently resistant to stress corrosion cracking.
In the case of stress corrosion cracking (SSC), H2S near the surface of the steel breaks down during the corrosion reaction into iron sulphides (FeS) and atomic hydrogen (H). This little hydrogen atom is so small that it can easily navigate into the iron crystals in the steel. When it finds a voids, welding porosity, slag inclusion, inclusions from dirty steel-making, etc. the hydrogen atom will prefer to stay there (since there is a little more room). When another hydrogen atom comes along, they prefer to hang out together and form hydrogen gas (H2). With enough exposure to H2S and more and more hydrogen atoms entering the steel, the hydrogen gas pressure increases in the voids in the steel until the steel cracks from the inside out (this is called HIC) or the stress on the steel combines with the stress from inside the steel to cause SSC.
The MR0175 spec wants to prevent SSC in downhole environments, storage batteries, desulphurization systems, piping systems, etc. which take the product up to the fence of the refinery. Beyond that, MR0175 doesn’t apply. For the years between 1975 and 2003, many engineers extrapolated the MR0175 concepts and applied them to the refinery situation (along with the help of RP0472, which even preceded MR0175 and addresses welding concerns and H2S cracking in refineries). The first issue of MR0103 in 2003 filled the gap.
Earlier editions of NACE MR0175 referred only to sour service applications, which lead to the common use of “this pipe meets NACE” without much need for further clarification.
The 2003 revision of the NACE MR0175 specification stipulates four different regions (confusingly named “Region 0” to “Region 3”), which are based on environmental factors including pH and the partial pressure of H2S. Region 0 is the least severe and includes a scenario where no H2S is present. Therefore, we can no longer say “this pipe meets NACE” because we may only be referring to Region 0 which is not at all sour service.
Region 3 is considered the most severe region, with a low pH (acidic) and a high partial pressure of H2S. When selecting materials for use in Region 3, only materials meeting the most strict requirements of Annex A, Clause A.2 of this specification may be used.
Annex A, Clause A.2.1 lists several requirements including the familiar hardness maximums of 22 HRC (248 HV max in weld zones), nickel content at a maximum of 1%, restrictions on the use of free-machining steels, and requiring heat treatments that would not result in high hardness. There are also restrictions on the use of proper welding procedures, surface treatments and cold work.
My company hot sale steel pipe and pipe fittings:
ASTM A106 B seamless pipes,(1” to 24” sch40, sch80),
API 5L GR.B steel pipes, (seamless pipe, LSAW pipe, SSAW pipes, 1” to 110” sch 40, sch80),
Boiler tubes,( 20G. 12Cr1MoVG, ASTM A335 P5, P9, P11),
ASTM A333 GR.6 seamless pipes, ( 1” to 24” sch40, sch80, sch160),
TP304/304L, TP316/TP316L, stainless steel pipes, (1” to 48” sch10, sch20, sch40, sch80),
You Might Also Like
-
large diameter Seamless Line Pipes API 5L GR.B 1016x25.4 mm 6 m length
-
St37 Seamless Tube 88.9mm Diameter
-
Seamless Steel Pipe ASTM A106 B NACE MR 0175 12IN SCH160
-
Seamless Line Pipe API 5L GR.B 24INCH SCH40 12M Length
-
Seamless Pipe 2inch Idimeter XXS 6 M LENGTH Export
-
Seamless Pipe ASTM A106 C 10IN Diameter XS 12M Length
Send Inquiry